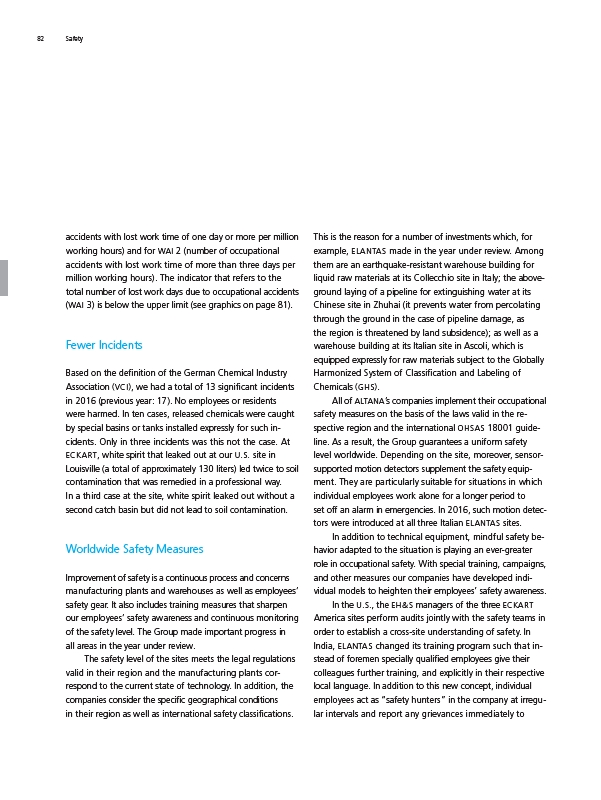
This is the reason for a number of investments which, for
example, ELANTAS made in the year under review. Among
them are an earthquake-resistant warehouse building for
liquid raw materials at its Collecchio site in Italy; the aboveground
laying of a pipeline for extinguishing water at its
Chinese site in Zhuhai (it prevents water from percolating
through the ground in the case of pipeline damage, as
the region is threatened by land subsidence); as well as a
warehouse building at its Italian site in Ascoli, which is
equipped expressly for raw materials subject to the Globally
Harmonized System of Classification and Labeling of
Chemicals
(GHS).
All of ALTANA’s companies implement their occupational
safety measures on the basis of the laws valid in the respective
region and the international OHSAS 18001 guideline.
As a result, the Group guarantees a uniform safety
level
worldwide. Depending on the site, moreover, sensor‑supported
motion detectors supplement the safety equipment.
They are particularly suitable for situations in which
individual employees work alone for a longer period to
set off an alarm in emergencies. In 2016, such motion detectors
were introduced at all three Italian ELANTAS sites.
In addition to technical equipment, mindful safety behavior
adapted to the situation is playing an ever-greater
role in occupational safety. With special training, campaigns,
and other measures our companies have developed individual
models to heighten their employees’ safety awareness.
In the U.S., the EH&S managers of the three ECKART
America sites perform audits jointly with the safety teams in
order to establish a cross-site understanding of safety. In
India,
ELANTAS changed its training program such that instead
of foremen specially qualified employees give their
colleagues
further training, and explicitly in their respective
local language. In addition to this new concept, individual
employees act as “safety hunters” in the company at irregular
intervals and report any grievances immediately to
82 Safety
accidents
with lost work time of one day or more per million
working hours) and for WAI 2 (number of occupational
accidents
with lost work time of more than three days per
million working hours). The indicator that refers to the
total
number of lost work days due to occupational accidents
(WAI 3) is below the upper limit (see graphics on page 81).
Fewer Incidents
Based on the definition of the German Chemical Industry
Association (VCI), we had a total of 13 significant incidents
in 2016 (previous year: 17). No employees or residents
were harmed. In ten cases, released chemicals were caught
by special basins or tanks installed expressly for such incidents.
Only in three incidents was this not the case. At
ECKART,
white spirit that leaked out at our U.S. site in
Louisville
(a total of approximately 130 liters) led twice to soil
contamination that was remedied in a professional way.
In a third case at the site, white spirit leaked out without a
second catch basin but did not lead to soil contamination.
Worldwide Safety Measures
Improvement of safety is a continuous process and concerns
manufacturing plants and warehouses as well as employees’
safety gear. It also includes training measures that sharpen
our employees’ safety awareness and continuous monitoring
of the safety level. The Group made important progress in
all areas in the year under review.
The safety level of the sites meets the legal regulations
valid in their region and the manufacturing plants correspond
to the current state of technology. In addition, the
companies consider the specific geographical conditions
in their region as well as international safety classifications.