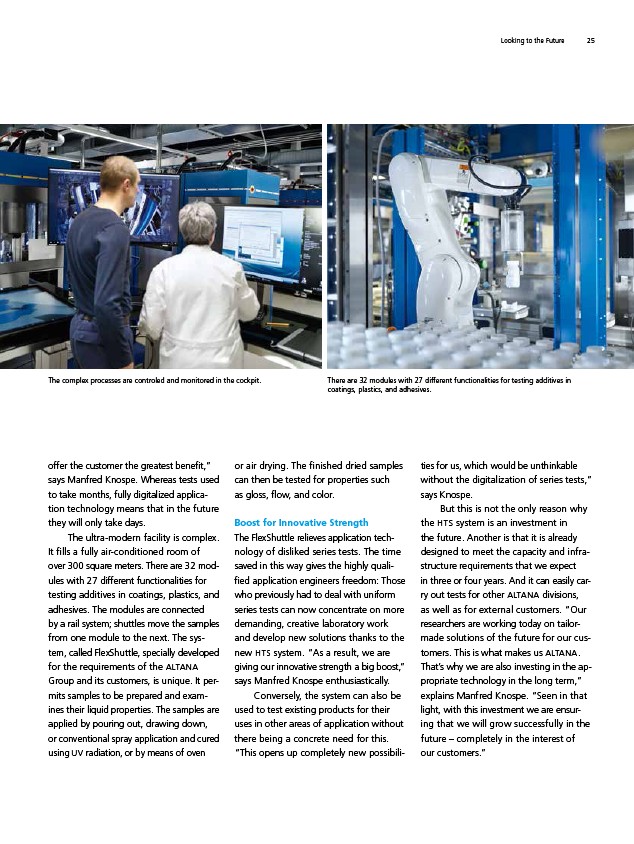
Looking to the Future 25
The complex processes are controled and monitored in the cockpit. There are 32 modules with 27 different functionalities for testing additives in
offer the customer the greatest benefit,”
says Manfred Knospe. Whereas tests used
to take months, fully digitalized application
technology means that in the future
they will only take days.
The ultra-modern facility is complex.
It fills a fully air-conditioned room of
over 300 square meters. There are 32 modules
with 27 different functionalities for
testing additives in coatings, plastics, and
adhesives. The modules are connected
by a rail system; shuttles move the samples
from one module to the next. The system,
called FlexShuttle, specially developed
for the requirements of the ALTANA
Group and its customers, is unique. It permits
samples to be prepared and examines
their liquid properties. The samples are
applied by pouring out, drawing down,
or conventional spray application and cured
using UV radiation, or by means of oven
coatings, plastics, and adhesives.
or air drying. The finished dried samples
can then be tested for properties such
as gloss, flow, and color.
Boost for Innovative Strength
The FlexShuttle relieves application technology
of disliked series tests. The time
saved in this way gives the highly qualified
application engineers freedom: Those
who previously had to deal with uniform
series tests can now concentrate on more
demanding, creative laboratory work
and develop new solutions thanks to the
new HTS system. “As a result, we are
giving our innovative strength a big boost,”
says Manfred Knospe enthusiastically.
Conversely, the system can also be
used to test existing products for their
uses in other areas of application without
there being a concrete need for this.
“This opens up completely new possibilities
for us, which would be unthinkable
without the digitalization of series tests,”
says Knospe.
But this is not the only reason why
the HTS system is an investment in
the future. Another is that it is already
designed to meet the capacity and infrastructure
requirements that we expect
in three or four years. And it can easily carry
out tests for other ALTANA divisions,
as well as for external customers. “Our
researchers are working today on tailor-
made solutions of the future for our customers.
This is what makes us ALTANA.
That’s why we are also investing in the appropriate
technology in the long term,”
explains Manfred Knospe. “Seen in that
light, with this investment we are ensur-
ing that we will grow successfully in the
future – completely in the interest of
our customers.”