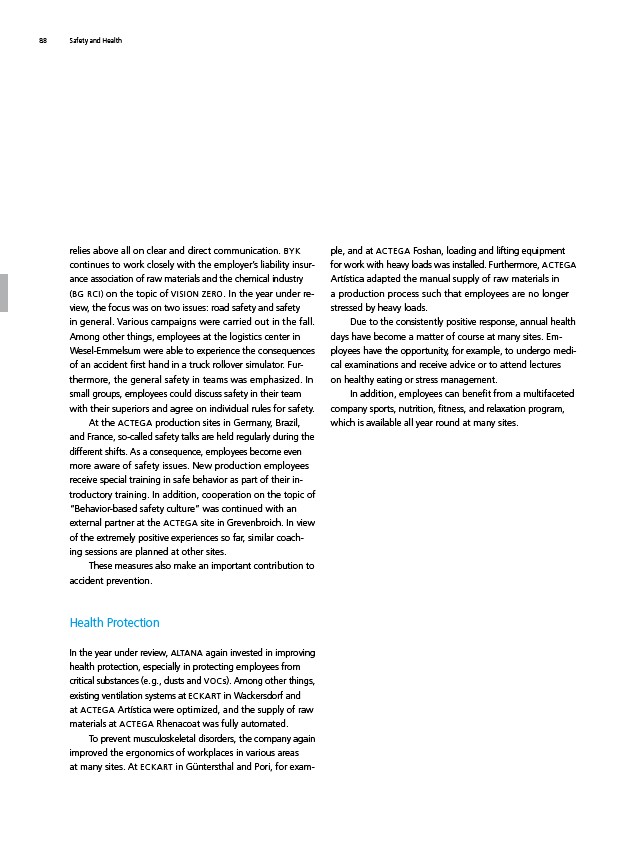
relies above all on clear and direct communication. BYK
continues to work closely with the employer’s liability insurance
association of raw materials and the chemical industry
(BG RCI) on the topic of VISION ZERO. In the year under review,
the focus was on two issues: road safety and safety
in general. Various campaigns were carried out in the fall.
Among other things, employees at the logistics center in
Wesel-Emmelsum were able to experience the consequences
of an accident first hand in a truck rollover simulator. Furthermore,
the general safety in teams was emphasized. In
small groups, employees could discuss safety in their team
with their superiors and agree on individual rules for safety.
At the ACTEGA production sites in Germany, Brazil,
and France, so-called safety talks are held regularly during the
different shifts. As a consequence, employees become even
more aware of safety issues. New production employees
receive special training in safe behavior as part of their introductory
training. In addition, cooperation on the topic of
“Behavior-based safety culture” was continued with an
external partner at the ACTEGA site in Grevenbroich. In view
of the extremely positive experiences so far, similar coach-
ing sessions are planned at other sites.
These measures also make an important contribution to
accident prevention.
Health Protection
In the year under review, ALTANA again invested in improving
health protection, especially in protecting employees from
critical substances (e. g., dusts and VOCs). Among other things,
existing ventilation systems at ECKART in Wackersdorf and
at ACTEGA Artística were optimized, and the supply of raw
materials at ACTEGA Rhenacoat was fully automated.
To prevent musculoskeletal disorders, the company again
improved the ergonomics of workplaces in various areas
at many sites. At ECKART in Güntersthal and Pori, for example,
and at ACTEGA Foshan, loading and lifting equipment
for work with heavy loads was installed. Furthermore, ACTEGA
Artística adapted the manual supply of raw materials in
a production process such that employees are no longer
stressed by heavy loads.
Due to the consistently positive response, annual health
days have become a matter of course at many sites. Employees
have the opportunity, for example, to undergo medical
examinations and receive advice or to attend lectures
on healthy eating or stress management.
In addition, employees can benefit from a multifaceted
company sports, nutrition, fitness, and relaxation program,
which is available all year round at many sites.
88 Safety and Health