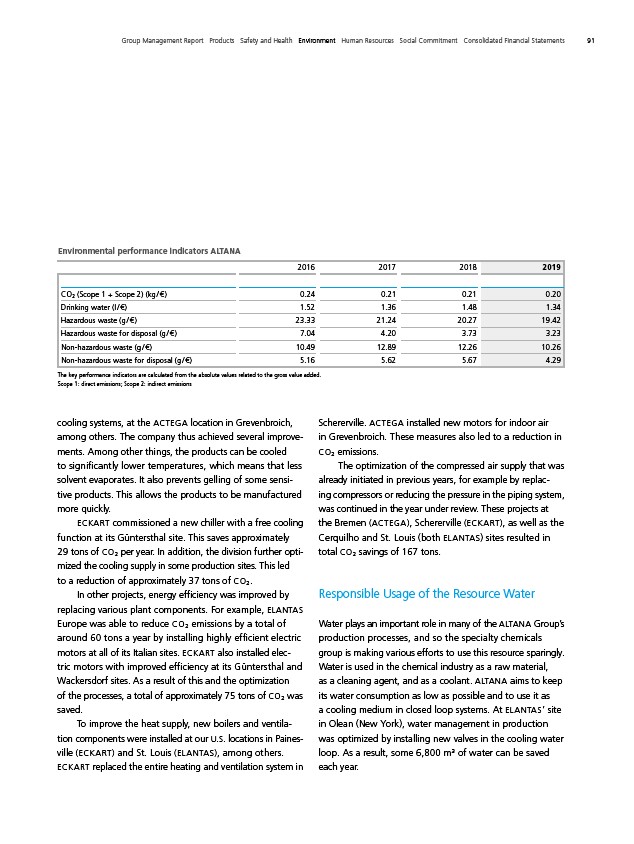
Group Management Report Products Safety and Health Environment Human Resources Social Commitment Consolidated Financial Statements 91
cooling systems, at the ACTEGA location in Grevenbroich,
among others. The company thus achieved several improvements.
Among other things, the products can be cooled
to significantly lower temperatures, which means that less
solvent evaporates. It also prevents gelling of some sensitive
products. This allows the products to be manufactured
more quickly.
ECKART commissioned a new chiller with a free cooling
function at its Güntersthal site. This saves approximately
29 tons of CO² per year. In addition, the division further optimized
the cooling supply in some production sites. This led
to a reduction of approximately 37 tons of CO².
In other projects, energy efficiency was improved by
replacing various plant components. For example, ELANTAS
Europe was able to reduce CO² emissions by a total of
around 60 tons a year by installing highly efficient electric
motors at all of its Italian sites. ECKART also installed elec-
tric motors with improved efficiency at its Güntersthal and
Wackersdorf sites. As a result of this and the optimization
of the processes, a total of approximately 75 tons of CO² was
saved.
To improve the heat supply, new boilers and ventilation
components were installed at our U.S. locations in Paines-
ville (ECKART) and St. Louis (ELANTAS), among others.
ECKART replaced the entire heating and ventilation system in
Schererville. ACTEGA installed new motors for indoor air
in Grevenbroich. These measures also led to a reduction in
CO² emissions.
The optimization of the compressed air supply that was
already initiated in previous years, for example by replac-
ing compressors or reducing the pressure in the piping system,
was continued in the year under review. These projects at
the Bremen (ACTEGA), Schererville (ECKART), as well as the
Cerquilho and St. Louis (both ELANTAS) sites resulted in
total CO² savings of 167 tons.
Responsible Usage of the Resource Water
Water plays an important role in many of the ALTANA Group’s
production processes, and so the specialty chemicals
group is making various efforts to use this resource sparingly.
Water is used in the chemical industry as a raw material,
as a cleaning agent, and as a coolant. ALTANA aims to keep
its water consumption as low as possible and to use it as
a cooling medium in closed loop systems. At ELANTAS’ site
in Olean (New York), water management in production
was optimized by installing new valves in the cooling water
loop. As a result, some 6,800 m³ of water can be saved
each year.
Environmental performance indicators ALTANA
2016 2017 2018 2019
CO² (Scope 1 + Scope 2) (kg / € ) 0.24 0.21 0.21 0.20
Drinking water (l / € ) 1.52 1.36 1.48 1.34
Hazardous waste (g / € ) 23.33 21.24 20.27 19.42
Hazardous waste for disposal (g / € ) 7.04 4.20 3.73 3.23
Non-hazardous waste (g / € ) 10.49 12.89 12.26 10.26
Non-hazardous waste for disposal (g / € ) 5.16 5.62 5.67 4.29
The key performance indicators are calculated from the absolute values related to the gross value added.
Scope 1: direct emissions; Scope 2: indirect emissions